Bayan for Manufacturing Operations Management
Bayan for Manufacturing Operations Management
Need Any Assistance?
We are here to help our customers at any time. You can call 24/7 to answer your question.
- +966122880564
- +966549000191
- support@bayanerp.com
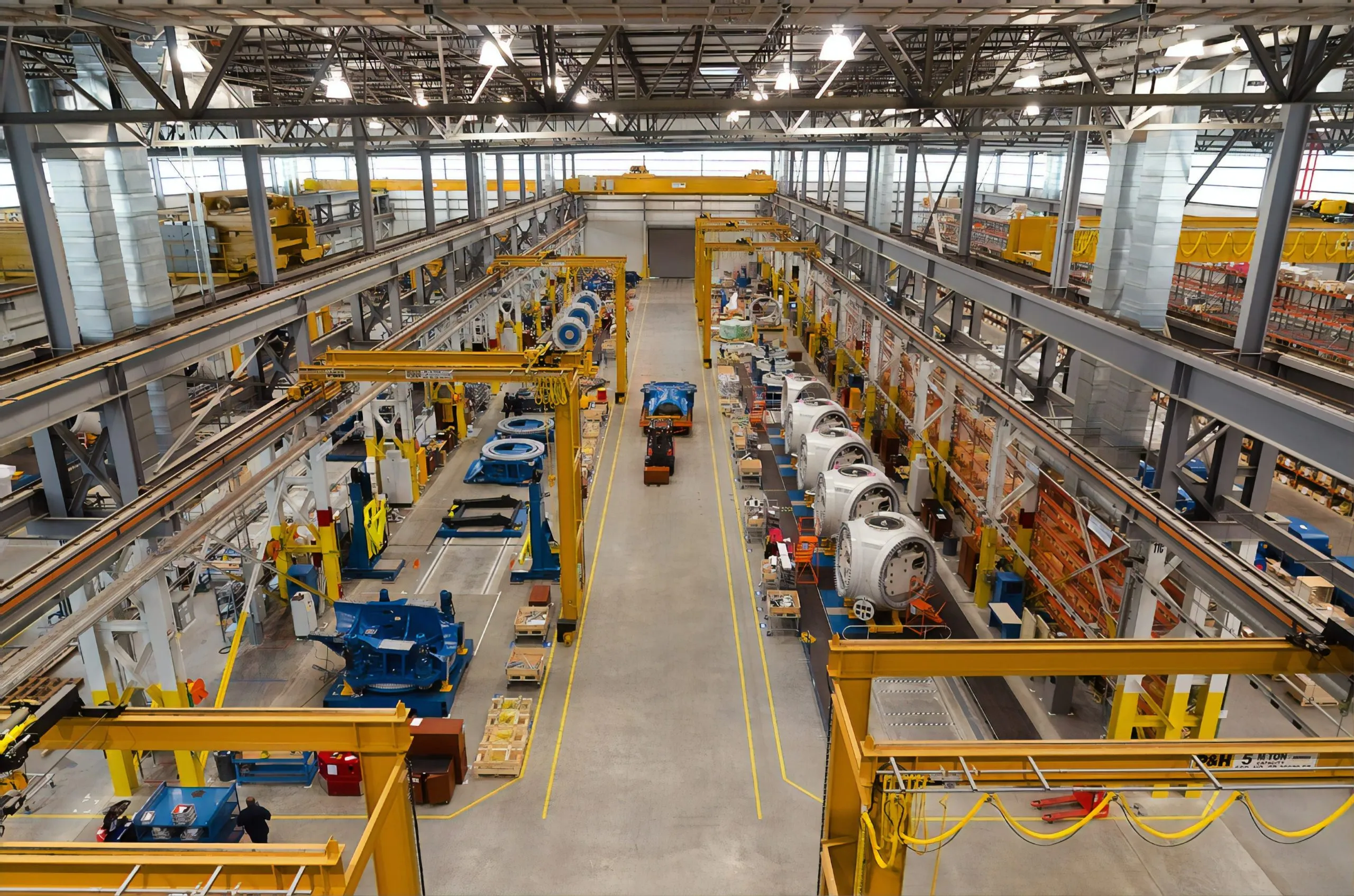
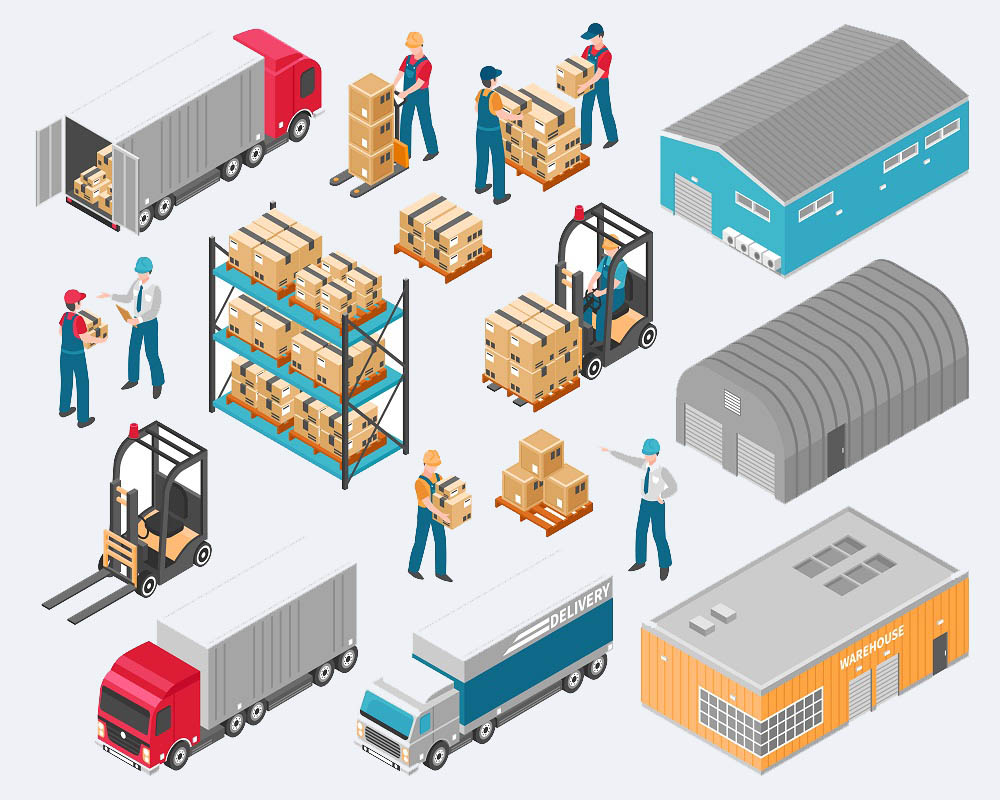

Introduction to the system
Bayan Factory Management System works to convert all operations in the various factory centers from information storage or document archiving and data exchange between different centers into a fully electronic process. Starting work by identifying the elements of indirect industrial costs, passing through the registration of all factory centers such as service and productivity, recording machinery data, and the system supports Multiple production lines and production methods, the system allows setting a budget for each of the factory centers and linking the centers with the accounts in the general ledger. It also monitors the quantities of raw materials used for each production order and the proportions of their use compared to the progress of production. The system also provides control over workers within the factory centers, each according to their specific tasks. In the worker’s work card, the system provides many ways to calculate the wages of workers in production lines (monthly salary – daily wages – hourly wages – wages according to productivity). These units are produced with the raw materials associated with the worker, and the system provides many reports for calculating the actual costs and comparing them with the estimated costs. The system also provides reports on the raw materials used and the quantities of the final product. and producing units.
Production Line Management
The system supports multiple production lines with complete management of all production requests within the production line.
A different sequence for all production orders within the production line.
The possibility of classifying production orders within the production line.
Production Workers
The system provides many options for manpower management in the factory, as it provides many options for calculating the cost of business
Provide a daily record of the worker’s operations in order to make the most of the workers’ time.
Distribution of materials at the level of workers within the factory.
Connecting workers in production to machines.
The possibility of calculating workers’ wages in daily wages, hourly wages, or the number of production units for the worker.
Indirect Costs
The ability to classify the indirect costs elements into an infinite number of elements, with each element linked to an account and a cost center within the general ledger
The possibility of defining production centers and service centers and distributing the indirect costs of service centers to production centers.
The possibility of determining an estimated budget for the elements of indirect costs, and with each period it is possible to print deviation reports between the actual and estimated costs.
Calculate the load rate for indirect costs.
Raw materials
The product is defined by identifying the raw materials used to obtain the final product.
Connecting raw materials with the departments, stages and processes within the production line.
Connecting raw materials with workers within the production line in order to achieve complete control over the raw stock.
Automatically configure the raw material request for each production order.
Configure the raw material exchange order automatically for each production order.
Supports the transfer of raw materials between different departments within the production order.
Supports raw material transfer between production orders.
The possibility of making an inventory of raw materials within each production order.
Determine the damaged or wasted quantities in the different sections of the factory.
Supports the transfer of costs of damaged or wasted raw materials to the accounts of the workers.
products
Flexibility in registering products and linking them with the warehouse system.
Ease of identifying the raw materials that are used in the production of the product.
Determine the stages, sections, processes and production line that the product goes through.
Determine which machines the product goes through.
Determine the estimated cost of the products once the production order is formed.
Supports linking products in each process to labor.
Raw material sorting
The system provides an easy mechanism for sorting raw materials before entering production lines, and this option is used in date factories.
The financial and inventory impact of sorting is formed automatically based on equations that are built with great flexibility by the sorting official.
The possibility of linking labor wages and indirect costs to sorting orders.
reports
reports
Productivity follow-up reports
Factory daily summary
Report of materials produced during a period
Report of raw materials consumed in production at the level of production order, section, stage, process or factory
Report working hours in production at the level of production order, department, stage, process, or factory
Production cost reports at the level of each product
Reports of indirect industrial costs at the level of each product, section, stage or process